AMADA FO 3015 NT LASER
The FO 3015 NT is engineered to meet the high quality and shorter lead time demands of today’s fabricating companies.
FEATURES:
- Maximize utilization with minimal setup between jobs.
- High speed processing of thin and thick materials.
- Operator-friendly windows-based network compatible control
- Performance-proven rack and pinion drive system in the X-axis and high-precision ball screws in the Y and Z axis.
- High-speed shuttle table design improves overall machine utilization by externalizing the material setup process.
- Cast iron frame for superior stability.
- Water Assisted Cutting System (WACS™) uses an adjustable water mist to absorb heat generated by the cutting process.
- Cut Process Monitoring for automatic pierce detection as well as plasma detection for thick stainless steel and aluminum.
- Interlocked enclosure surrounds cutting area to ensure safety.
- AMADA/FANUC RF excited resonator provides unmatched performance and reliability.
- Automation ready.
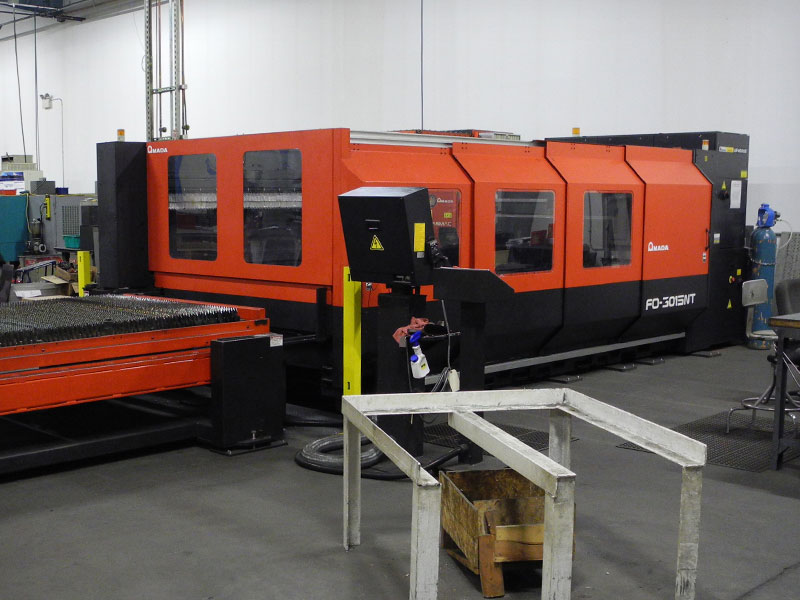
AMADA HS 1303 PRESS BRAKE
Built on the solid foundation of the HFE M2 Series, Amada’s HS press brake series includes additional production-enhancing features and an innovative touchscreen NC Control. Overall design improvements result in an eco-friendly series that provide maximum performance and ease of use. Equipped with an energy saving drive — the inverter on the HS series reflects Amada’s ongoing commitment to environmental protection. The new drive system uses a frequency inverter that controls the motor pump and ensures efficiency by operating only when necessary. The system continually monitors and self-regulates bending requirements — this translates to using 20% less energy, a significant reduction in maintenance requirements, less oil consumption, lower noise levels and an increase in reliability.
FEATURES:
- Numeric Control (NC) – The AB PAD is equipped with an intuitive touchscreen interface. Users can also remotely monitor the operation of the machine, transfer programs and perform diagnostics.
- Multiple Axis Backgauge – The light weight but rigid design allows for high speed and precise positioning. With the gauging capacity of up to 40”, large components can be easily processed. In the 6-axis version, the modules L1 L2 and Y1 Y2 are programmable independently, offering greater backgauge flexibility.
- SGRIP Punch Holders – Allows the brake operator to change punches on the press brake quickly and safely without requiring a wrench. The patented SGRIP design dramatically decreases tool changeover time, thereby increasing bending productivity.
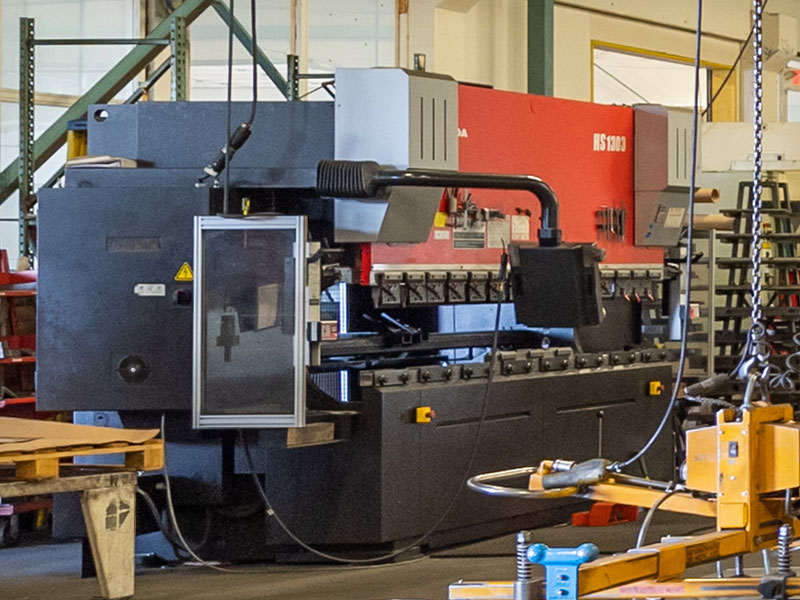
HURCO TMM10 LATHE
The TMM mill turn machines are true slant-bed lathes equipped with live tooling. These lathes are perfect for small to medium lot sizes that require turning and secondary milling/drilling operations. Saving time with one setup and improving accuracy without the need to refixture.
FEATURES:
- 3” through spindle bore with 11.6” maximum turning diameter.
- 12 station live/static tooling turret allows milling operations as well as standard turning and boring.
- Multiple operations in one machine improves overall part accuracy.
- Constant surface speed for superior part finish and optimum tool life.
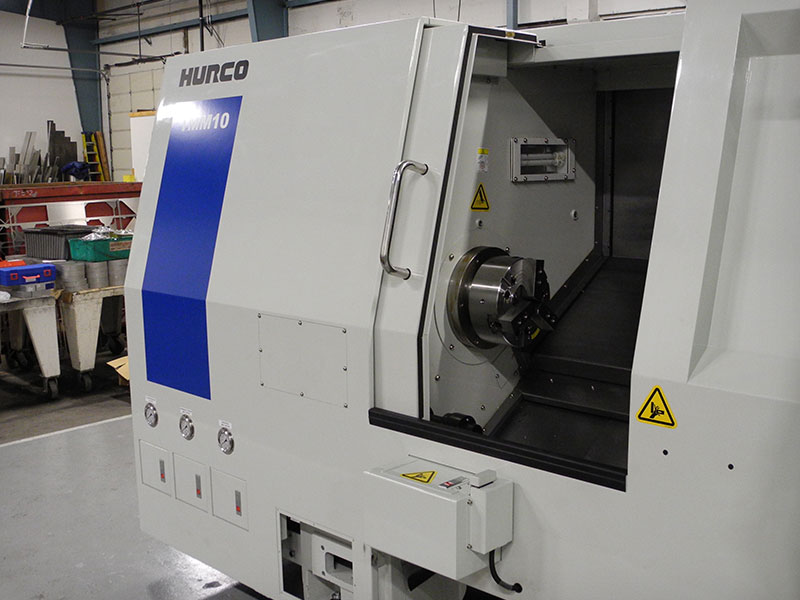
HYD-MECH H-12A CUT-OFF SAW
FEATURES:
- 12” x 12” capacity.
- Automatic programmable feed system for precise and repeatable cuts.
- Extended in feed bed allows 22′ material lengths.
- Variable blade speed helps optimize cutting a wide variety of materials.
- Vises are extremely heavy duty and feature a 40” shuttle with multi-indexing capability.
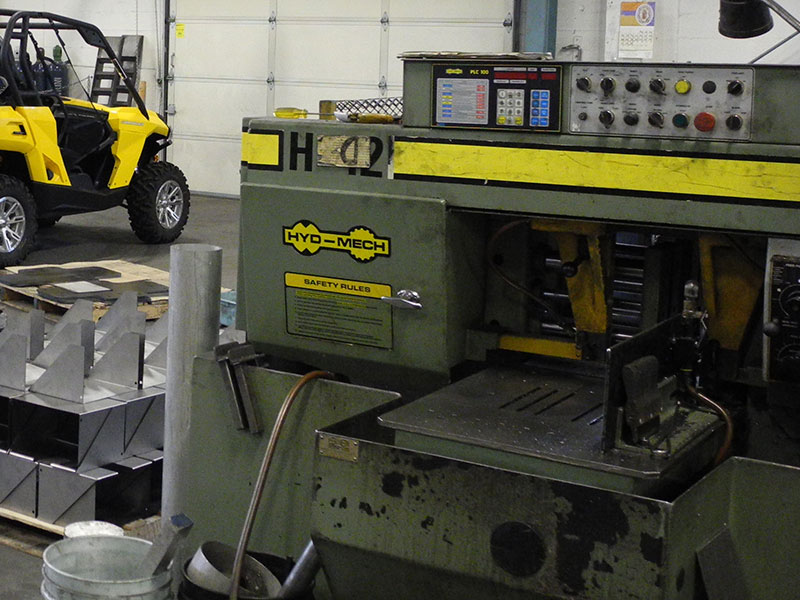